В Санкт-Петербурге создали пластик будущего, который можно применять в абсолютно любой отрасли
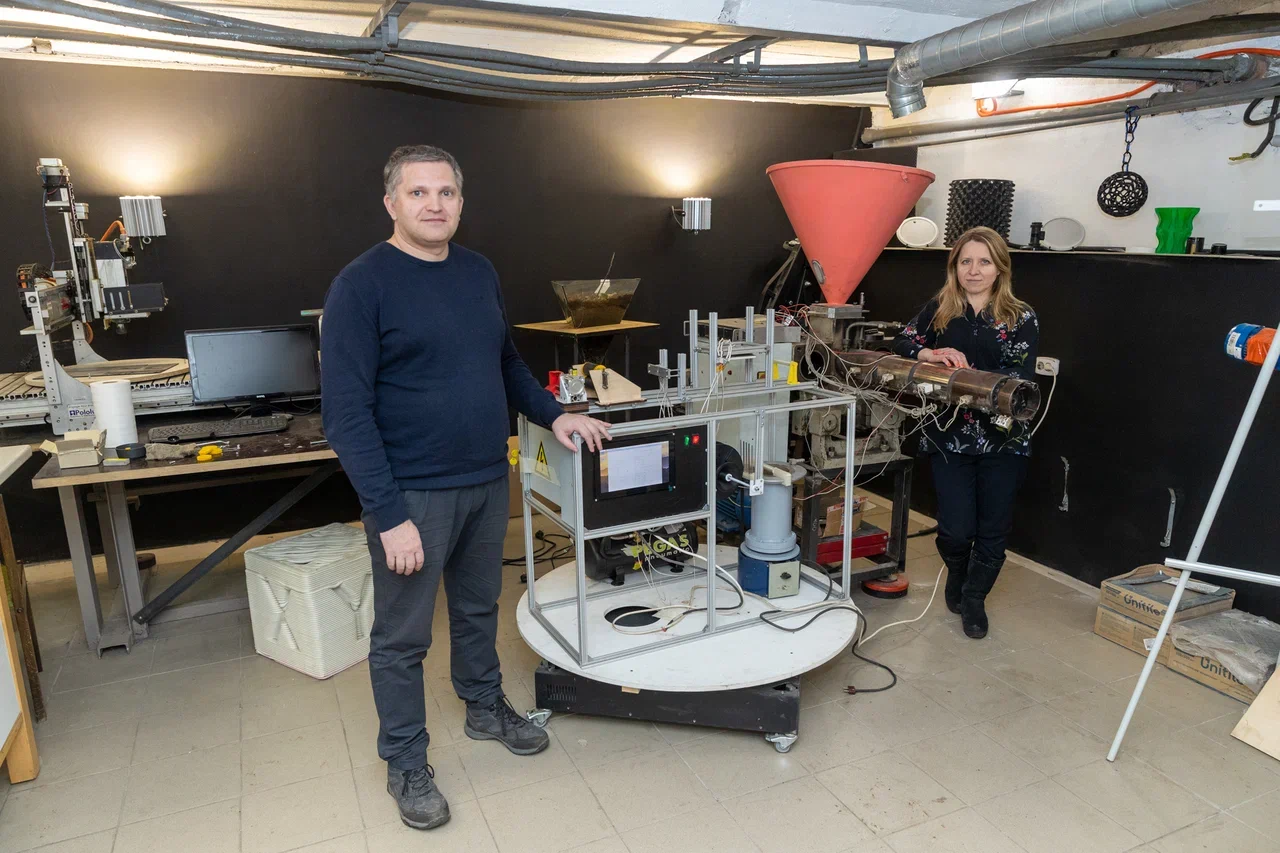
Ученые изобрели и запатентовали устройство для получения необычного пластика, который можно использовать в абсолютно любой отрасли от машиностроения до медицины, заменив металлы, дерево и даже кости человека. Изделия из нового композита изготавливать проще, дешевле и технологичнее, чем из других материалов. Разработкой занимались ученые и студенты Санкт-Петербургского политехнического университета Петра Великого (СПбПУ) совместно с ведущими российскими экспертами по полимерным материалам Института высокомолекулярных соединений РАН.
Уникальный пластик получается в процессе смешивания двух компонентов. Порошковый полимер электрически заряжается и превращается в псевдожидкость. Через нее пропускаются углеродные волокна, которые облепляют частицы порошка. После чего эта масса плавится, превращаясь в похожую на мед густую жидкость, и твердеет. На выходе получаются гранулы композита, близкого по физическим свойствам к железобетону.
«Пластик в композите отвечает за сжатие, а волокна — за растяжение. Стандартные технологии позволяют добавлять волокна, которые разрублены на мелкие кусочки, длиной в доли миллиметров — 300 микрон и даже меньше — это делается для равномерного распределения по материалу. Нам удалось увеличить длину волокон до нескольких миллиметров, тем самым придав материалу отличную прочность, сопоставимую с металлами», — рассказал ведущий научный сотрудник научно-образовательного центра «Биомеханики и медицинской инженерии» СПбПУ Игорь Радченко.
Изделия из уникального пластика можно изготавливать теми же методами, с помощью которых получают практически все пластмассовые предметы, в том числе литьевым прессованием и литьем под давлением. Гранулы композита также можно преобразовать в филамент — нить для 3D-печати. Ученые СПбПУ уже напечатали на 3D-принтере несколько пробных деталей, которые используют для изучения и описания физических характеристик нового материала.
Изделия из нового композита изготавливать проще, дешевле и технологичнее, чем из других материалов. Например, металлы очень дороги в обслуживании и ремонте, а пластик петербуржских ученых ремонтировать практически не придется. Кроме того, за счет использования аддитивных технологий можно выпускать малые тиражи деталей и разные прототипы без сложной перенастройки используемого оборудования.
«Мы разработали материалы и технологии их производства, из которых можно создать даже блок цилиндров для двигателя внутреннего сгорания. Он будет в разы дешевле и легче, его проще обрабатывать, сверлить в нем отверстия, создавать каналы для охлаждения», — отметил Игорь Радченко.
Использовать новый материал можно практически в любой сфере: машиностроении, авиастроении, судостроении, газовой и нефтяной промышленности, для создания космической техники и оборудования для общего и специального назначения. Одним из самых востребованных сценариев применения такого пластика станет изготовление медицинских протезов и имплантов. Благодаря легкому весу и физическим свойствам, из композита можно сделать точную копию костей человека.
Разработка велась в рамках программы Минобрнауки России «Приоритет 2030», которая является одной из мер государственной поддержки университетов нацпроекта «Наука и университеты».